式中,伪蓄热体摩擦阻力系数;p。为流体密度;8为蓄热体的孔隙率;v。为表观速度;D。为当量直径;K-为进口压力损失系数,蜂窝陶瓷蓄热体为1.04;K'‘为出口压力损失系数,蜂窝陶瓷蓄热体为-0.3;L为蓄热体长度。
1.2试验系统
蜂窝陶瓷阻力特性实验台主要包括配风系统、蓄热室、监测控制系统三部分。实验台主要由风机、流量调节阀、燃烧器、蓄热室、微压差变送器、热电偶及保温材料组成。蜂窝陶瓷蓄热体阻力特性实验台结构如图2所示。实验台工作流程为:打开风机5,6,点燃燃烧器,调节阀7,8调节风机进入混风室的风量,在混风室试验要求的流量温度稳定的热风。混风室内形成的热风流过蓄热室,加热蜂窝陶瓷蓄热体,终由排气尾管将尾气排出。通过调节流量阀9可以有效尾气温度过高。蓄热室两端的微压计将测得的流体流经蓄热体时产生的压力降和热电偶组测得的蓄热体温度传递给监测控制系统,监测控制系统则对数据进行实时保存处理。
1.3试验对象
本文主要研究蜂窝陶瓷蓄热体长度、孔隙率以及流速变化对蓄热体压力损失的影响,实验所用莫来石蜂窝陶瓷的主要参数如表l所示。
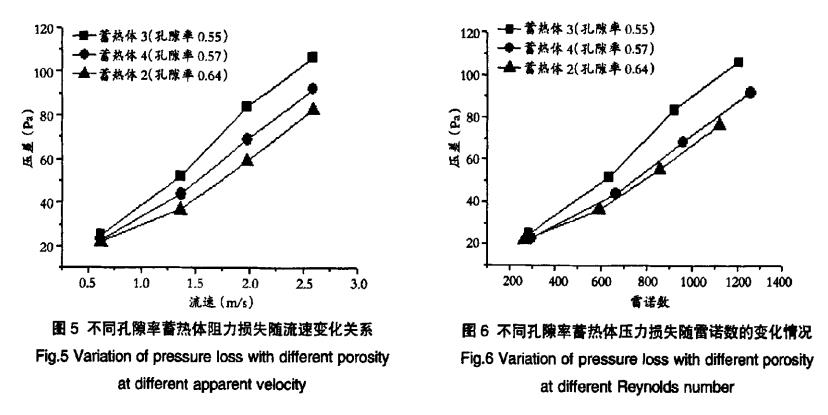
2试验结果与分析
2.1陶瓷蓄热体长度对阻力损失的影响图3和4为不同表观流速下蓄热体长度变化对阻力损失的影响。
由图3可知,在相同表观流速下,蓄热体内气体压力损失随蓄热体长度增加而增加。在相同蓄热体长度下,蓄热体内气体压力损失随气体流速的增加而变大。由图4可知:在相同雷诺数下,蓄热体内压力损失随着蓄热体长度的增加而增加,在相同蓄热体长度下,蓄热体内压力损失随雷诺数的增加而增加。在蓄热体长度小于300mm、雷诺数小于600时,蓄热体内压力损失变化比较大,呈不规则增加,在蓄热体长度大于300ram、雷诺数大于600时,蓄热体内压力损失随蓄热体长度变化呈现出较好的线性增加趋势。这主要是因为蓄热体长度较短、雷诺数较低时,流体流速较低,且处于流动入口段。这时入口段效应比较明显,蓄热体局部压力损失当然也就越大,ilP Ap。在总压降中的比例增加。但随着蓄热体长度的增加,表观流速增加,入口段效应逐渐减弱,并且对于—给定的流道,在一定流速下,入I:1段长径比是一个定值,而且入口段效应主要集中在进口区域,随着流道长度的,△p在总压降中的比例增加,实验表明当蓄热体长度超过300ram时,对于蜂窝陶瓷蓄热体入口段效应可以忽略。
2.2孔隙率对阻力损失的影响
孔隙率是影响载体内气体压力损失的一个复杂因素。孔隙率在数值于蓄热体表面孔的内边长与外边长的平方比。因此,改变孔边长,蓄热体的孔隙率也会做相应改变。而即使孔边长相同,由于不同的孔型对蓄热体的阻力损失也会产生一定影响,所以为得出蓄热体孔隙率对蓄热体内压力损失的影响关系,实验在保持蓄热体材质、孔型不变的情况下,选用不同孔隙率的蓄热体进行相关实验。图5为不同表观流速下蓄热体阻力损失与蓄热体孔隙率之间的关系。
由图5可知在蓄热体孔型一定的情况下,蓄热体内压力损失随着流速的而。在相同流速下,蓄热体体内气体压力损失随着载体的孔隙率的增加而变小,这是因为在孔型和蓄热体横截面积一定时,随着蓄热体孔隙率,蓄热体的当量直径也会有所增加。蓄热体当量直径的增加使蓄热体内气体的流通性能,并且蓄热体的沿程阻力损失与蓄热体的当量直径在理论上成反比。图6为不同孔隙率蓄热体压力损失随雷诺数的变化情况,由图可知,其压力损失随蓄热体孔隙率的变化规律与图6中压力损失随气体流速之间的变化规律相—致。
2.3陶瓷蓄热体摩擦阻力系数实验关联式
蜂窝陶瓷的摩擦阻力系数受孔隙率、表观流速、当量直径等因素的影响,关系复杂。经化简式(2)可表示为式(3):
综合以上多种不同参数的蜂窝陶瓷蓄热体实验
研究所得到的数据,采用小二乘法处理实验数据,得出蓄热体摩擦阻力系数的实验关联式为:

从图7中以看出,实验关联式计算值与实验数据相吻合,数据偏离关联式算术平均偏差为9.60%。关联式适用于孔隙率为50%一70%,当量直径为2mm一4mm,陶瓷长度为100mm一600ram,Re为200—12000
3结论
(1)蜂窝陶瓷阻力损失随蓄热体长度增加而。在蓄热体长度一定时,蓄热体阻力损失随雷诺数增加而。
(2)蓄热体阻力损失随孔隙率增加而减小。在蓄热体孔隙率—定时,蓄热体阻力损失随雷诺数增加而。
(3)同一蓄热体阻力损失随气体流速增加而。
(4)根据实验数据得到了莫来石蜂窝陶瓷蓄热体摩擦阻力系数的实验关联式,为煤矿乏风氧化装置的设计提供了数据支持。